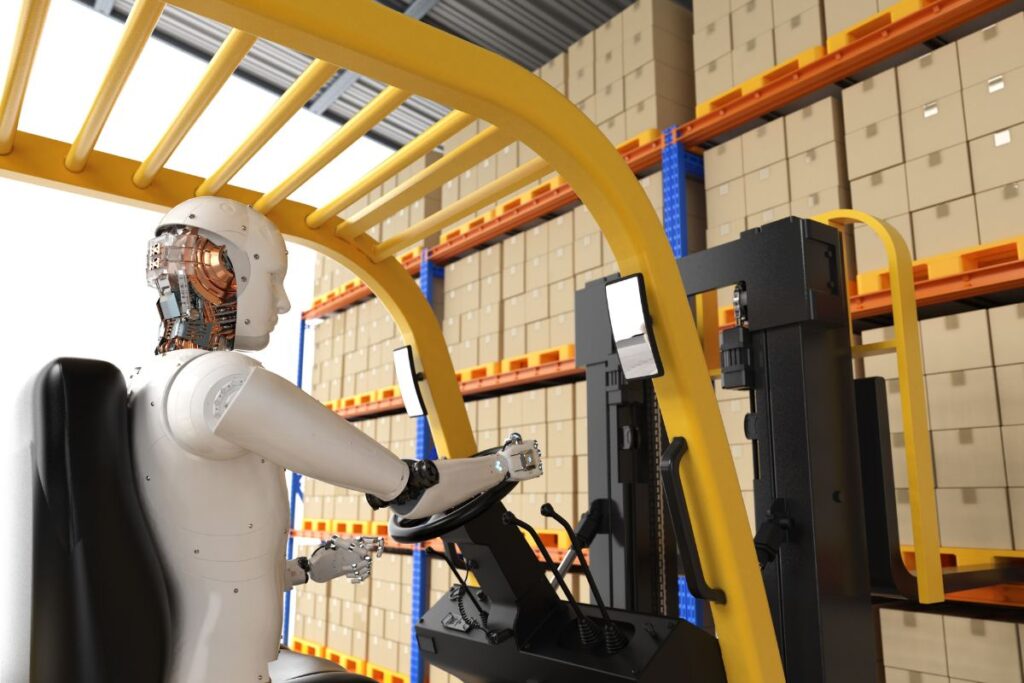
Warehouse management plays a pivotal role in the smooth functioning of supply chains, and its efficiency directly impacts a company’s ability to meet the demands of an ever-evolving market. As businesses strive for quicker order fulfilment and increased precision in inventory management, the integration of robotics in warehouse operations emerges as a revolutionary solution.
This blog post explores the current challenges in warehouse management, the rising importance of robotics, and the potential transformation it brings to logistics.
I. The Current Challenges in Warehouse Management
Traditional warehouse processes face significant challenges. Let us look into the obstacles that robotics aims to overcome in the pursuit of streamlined logistics.
- Labour Shortages and High Turnover Rates: The logistics industry faces an ongoing challenge of labour shortages and high turnover rates, leading to operational disruptions and increased costs. Human labour, while crucial, has limitations in meeting the escalating demands of modern commerce.
- Inefficiencies in Traditional Warehouse Processes: Traditional warehouse processes often suffer from inefficiencies, manual errors, and delays. These bottlenecks hinder the agility required to adapt to dynamic market conditions and consumer expectations.
- Increased Consumer Demand and Quick Order Fulfillment: The surge in e-commerce and consumer expectations for rapid order fulfilment exert additional pressure on warehouses. Manual processes struggle to keep pace, prompting the need for innovative solutions.
- The Impact of Human Error on Inventory Management: Human error remains a significant factor affecting inventory accuracy. Misplaced items, picking errors, and inaccuracies in stock levels can lead to customer dissatisfaction and financial losses.
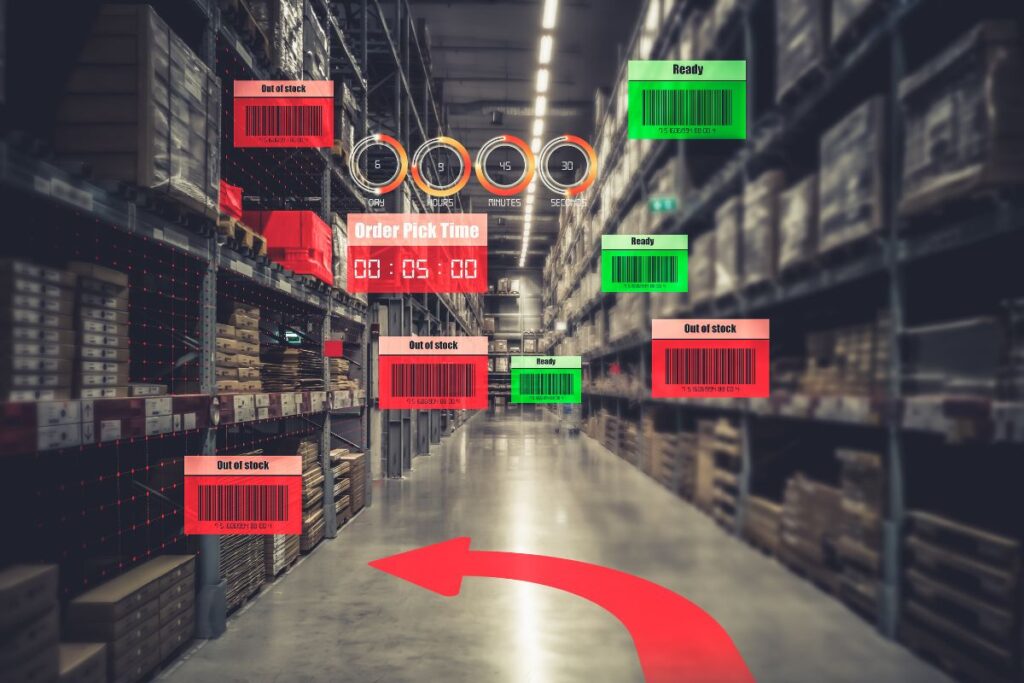
II. The Rise of Robotics in Logistics
As technology advances, various types of robotics are revolutionising warehouse operations. From AMRs to drones, this section outlines the diverse robotic solutions contributing to the evolution of logistics.
- Autonomous Mobile Robots (AMRs): AMRs navigate autonomously within warehouse environments, optimising the movement of goods and reducing the need for manual transport.
- Automated Guided Vehicles (AGVs): AGVs follow predetermined paths, handling material transportation efficiently. They contribute to the automation of routine tasks, allowing human workers to focus on more complex responsibilities.
- Robotic Arms and Pick-and-Place Systems: Robotic arms excel in tasks requiring precision and repetition, such as picking and placing items on shelves. These systems enhance speed and accuracy in the order fulfilment process.
- Drones for Inventory Tracking: Drones provide real-time visibility into warehouse inventory, enabling efficient monitoring and management of stock levels.
III. Advantages of Robotic Integration in Warehouse Management
The integration of robotics brings a multitude of advantages to warehouse management. Let’s look into the top benefits of the same.
Increased Efficiency and Productivity
Robotics streamline warehouse processes, reducing lead times and increasing overall operational efficiency. Automation allows warehouses to handle higher volumes with greater speed.
Reduction in Labour Costs and Dependence
While not replacing human workers, robots reduce the reliance on manual labour for routine tasks, leading to cost savings and resource optimisation.
Enhanced Accuracy in Order Fulfillment
The precision of robotic systems minimises errors in order picking and packing, contributing to higher customer satisfaction and reduced returns.
Real-Time Data and Analytics for Decision-Making
Robotics generate valuable data, providing insights into warehouse operations. This data-driven approach enhances decision-making and strategic planning.
Improved Workplace Safety
Robotics handle physically demanding and hazardous tasks, reducing the risk of workplace accidents and ensuring a safer environment for human workers.
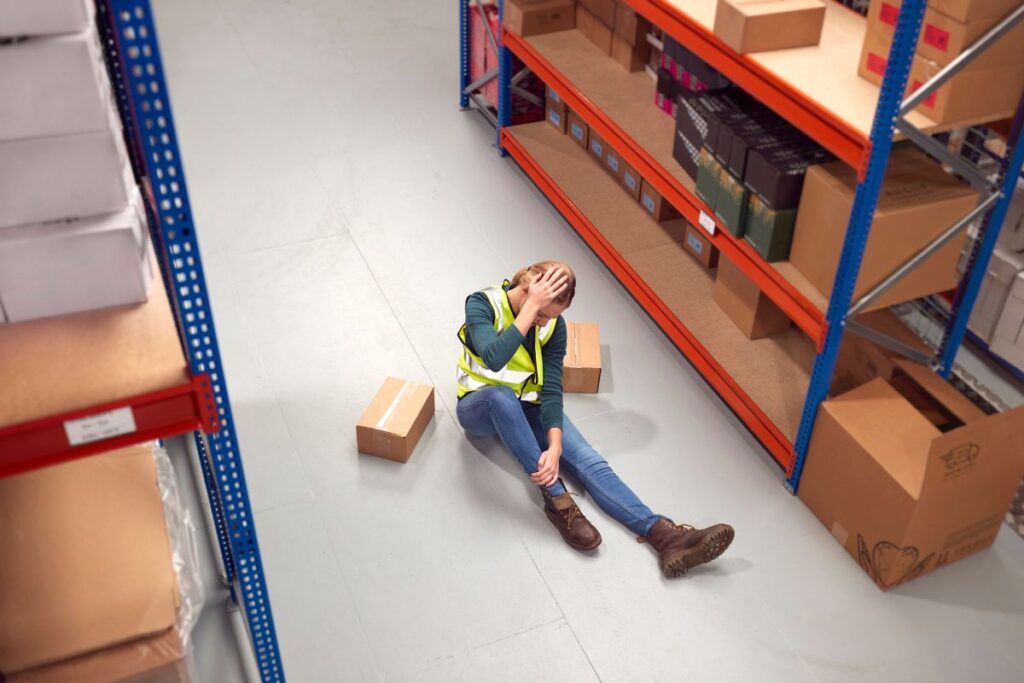
IV. Overcoming Challenges in Implementing Robotics
Implementing robotics in warehouses opens the door to a world of efficiency, but it’s not without its challenges. Let’s explore strategies to tackle these hurdles head-on.
Initial Costs and Return on Investment
Investing in robotics is like planting a seed. This section delves into the initial costs and why businesses need to view it as an investment rather than an expense:
- Navigating the Initial Investment: In the context of warehouse robotics, the initial investment involves not only the robotics systems but also the infrastructure modifications required for seamless integration. This includes evaluating costs related to installation, reconfiguration of warehouse layouts, and connectivity.
- Calculating Return on Investment (ROI): For warehouse managers, determining the return on investment is critical. The ROI calculation extends beyond traditional metrics and includes factors such as increased order fulfilment speed, reduced errors in inventory management, and the potential for round-the-clock operations.
- Exploring Financing Options: Given the capital-intensive nature of implementing robotics in warehouses, businesses must explore financing options tailored to the logistics industry. Collaborating with financial institutions or leveraging government incentives can significantly alleviate the initial financial burden.
Workforce Training and Integration
It’s not just about the robots; it’s about the humans too. This section focuses on the crucial aspect of workforce training and integration:
- Comprehensive Training Programs: Warehouse employees must undergo comprehensive training programs tailored to the nuances of working alongside robotic systems. Training should cover operational aspects, maintenance procedures, and collaborative workflows.
- Emphasising Human-Robot Collaboration: The warehouse environment thrives on the collaboration between human workers and robotic systems. Emphasising this collaborative aspect not only eases integration but fosters a positive mindset shift among employees.
- Fostering a Culture of Innovation: In a warehouse setting, fostering a culture of innovation is crucial. This involves not only technological training but also cultivating a mindset of continuous improvement and adaptability to technological advancements.
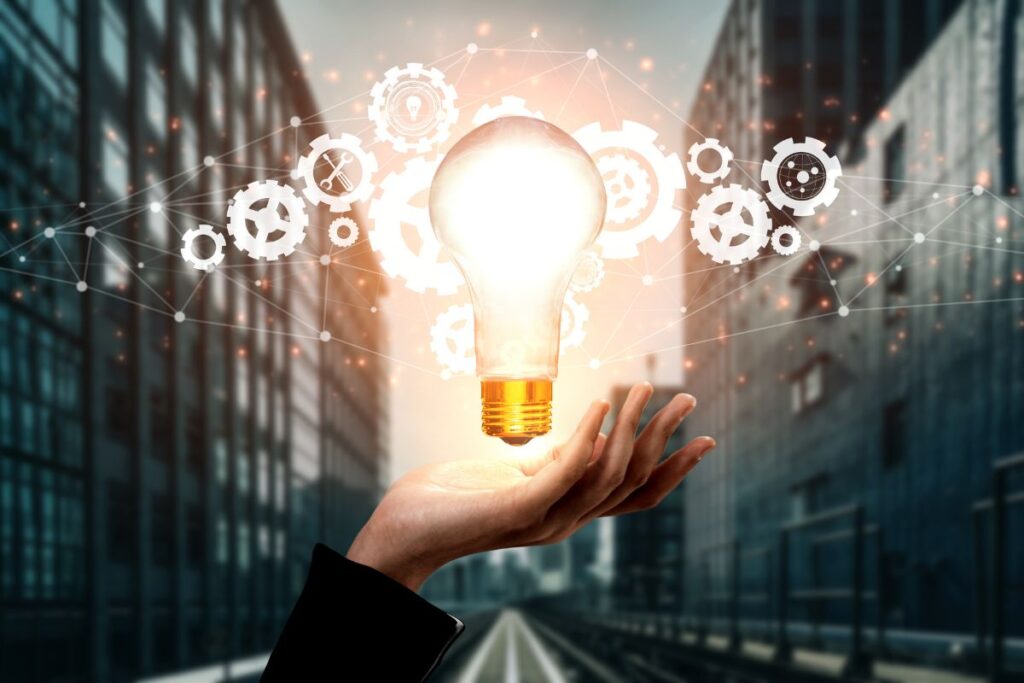
Addressing Concerns About Job Displacement
Robots and humans can coexist harmoniously. This part addresses concerns about job displacement and emphasises the positive aspects:
- Communication and Transparency: Warehouse staff may express concerns about job displacement with the introduction of robotics. Transparent communication is key, articulating that the goal is to enhance job roles, allowing humans to focus on tasks that require creativity, problem-solving, and decision-making.
- Skill Upgradation Opportunities: Addressing concerns involves providing skill upgradation opportunities. Collaborate with educational institutions or professional training programs to equip warehouse employees with skills that complement and enhance robotic operations.
- Creating Redeployment Programs: Establishing redeployment programs is vital. Identify areas within the warehouse where human skills are irreplaceable and create opportunities for employees to transition into roles that leverage their expertise alongside robotic systems.
Customisation and Scalability of Robotic Systems
One size doesn’t fit all in the world of robotics. This section sheds light on why customisation and scalability are critical:
- Scalability Planning: In the context of warehouse management, scalability planning is essential. Select robotic systems that can seamlessly scale with the evolving demands of the warehouse, accommodating fluctuations in order volumes and operational complexities.
- Customisation for Specific Tasks: Warehouses have diverse operational needs. Customising robotic solutions for specific tasks – be it order picking, packing, or inventory management – ensures that the technology aligns with the unique requirements of the logistics operations.
- Flexible Integration with Existing Systems: Compatibility with existing warehouse management systems is critical for successful integration. Robotic systems should integrate flexibly with these systems, minimising disruptions and maximising efficiency.
Navigating the challenges of implementing robotics requires strategic thinking and a collaborative approach. By addressing initial concerns and planning for the future, businesses can embrace the transformative power of robotics in warehouses.
V. The Future Landscape of Robotics in Warehouse Management
Looking ahead, let’s explore what the future holds for warehouse management. Exciting changes are on the horizon.
Emerging Technologies and Innovations
Imagine a world where robots get even smarter! We’re talking about making robots better by using things like artificial intelligence, machine learning, and the Internet of Things. This will help them work more efficiently and be super adaptable.
Collaborative Robotics: Teaming Up with Humans
In the future, humans and robots will team up like superheroes working together. Instead of robots doing everything on their own, they’ll team up with us to get things done faster and better.
Potential Impact on Supply Chain Networks
Think of the supply chain network like a big team passing the baton. When robots join in, it’s like giving the team a turbo boost. The whole system becomes more flexible and quick to respond to what’s needed. It’s like magic, but with robots!
VII. Industry Trends and Innovations
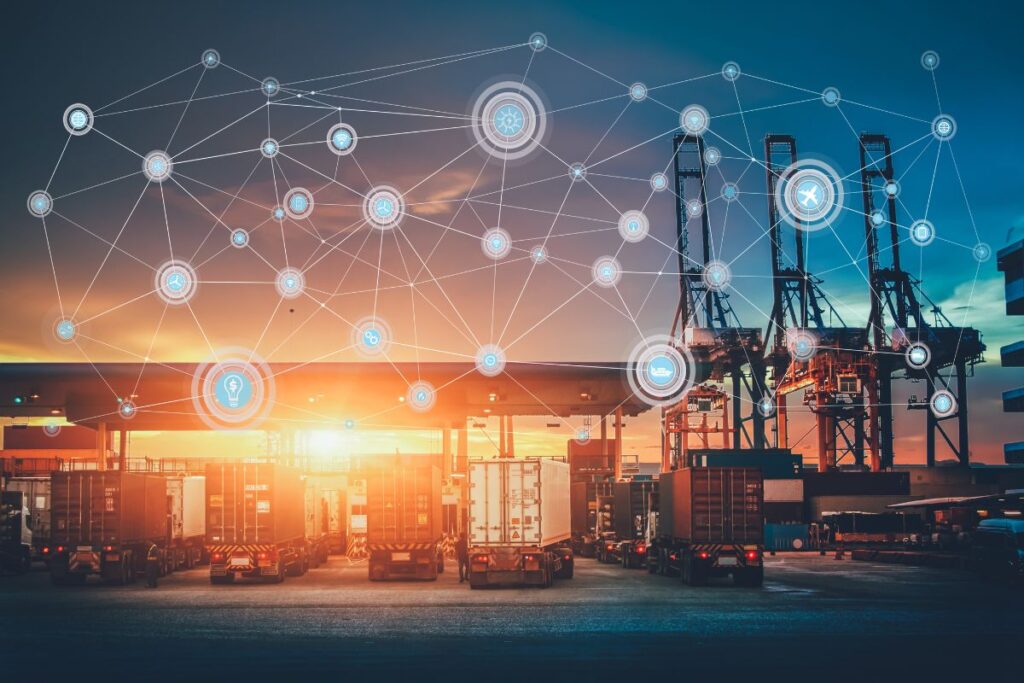
The evolving landscape of robotics in logistics is marked by key industry trends and innovations shaping the future of warehouse management.
Customisation and Flexibility
- Robotics trends emphasise customisation, allowing tailored solutions for diverse industries and warehouse setups.
- Flexibility in robotic systems enables optimisation, fostering efficiency and adaptability.
Collaborative Robotics (Cobots)
- The rise of collaborative robotics (cobots) enhances human-machine collaboration for increased efficiency.
- Cobots excels in tasks requiring a blend of human dexterity and robotic precision.
Innovations and Partnerships
- Last-mile delivery solutions, incorporating drones and autonomous vehicles, redefine the final stages of delivery.
- Integration of augmented reality (AR) and virtual reality (VR) transforms training and operational processes.
Sustainable and Eco-Friendly Initiatives
- The industry focuses on energy-efficient robotics and eco-friendly materials to reduce environmental impact.
- Warehouses adopt green technologies, aligning with sustainability goals.
As warehouses embrace these trends and innovations, they position themselves at the forefront of a dynamic and responsive logistics ecosystem, driving efficiency, collaboration, and sustainability.
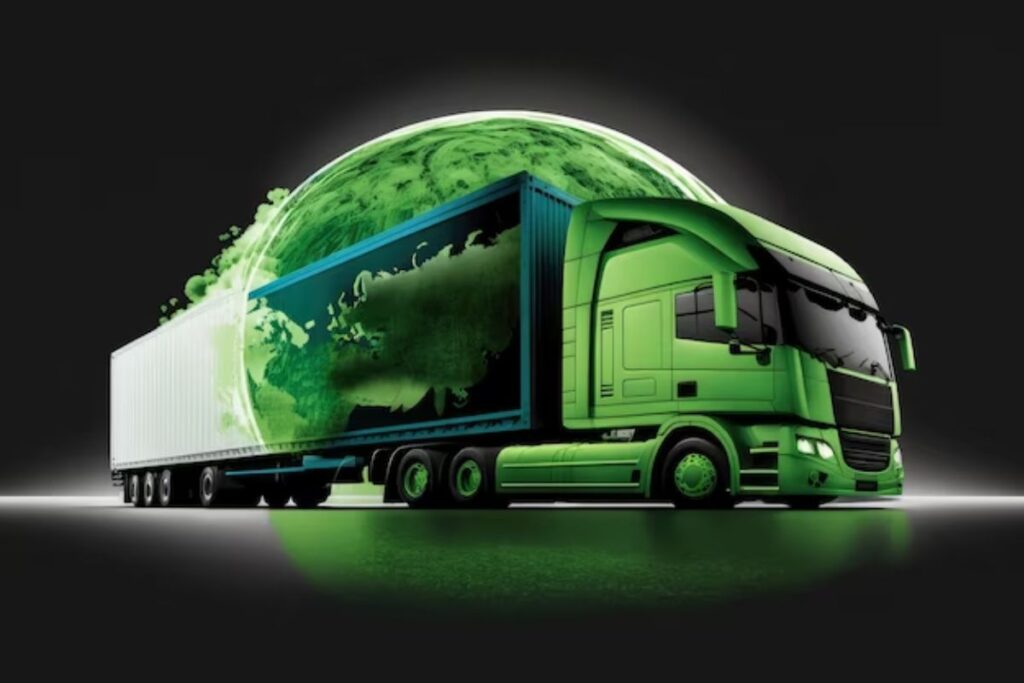
VII. Conclusion
In conclusion, the integration of robotics in warehouse management represents a paradigm shift in how businesses handle logistics. By addressing current challenges, realising the advantages of robotic integration, and considering the future landscape, companies can position themselves for success in an increasingly competitive market.
Embracing this transformative technology is not just about efficiency; it’s about shaping the future of logistics for the better. It’s a call to action for businesses to explore, adopt, and adapt to the evolving landscape of warehouse management.